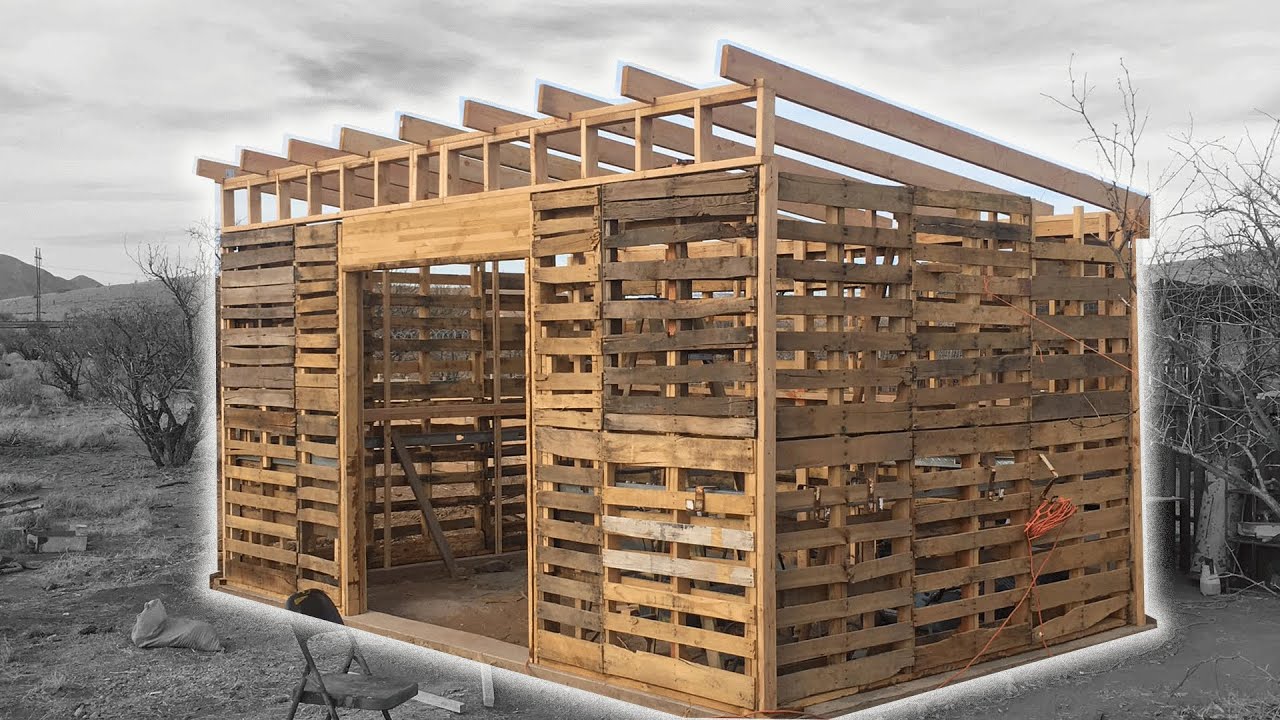
Build Your Dream Backyard Shed from Reclaimed Wood Pallets
Transform discarded wood pallets into a charming and functional backyard shed! This project is perfect for DIY enthusiasts seeking a cost-effective and eco-friendly storage solution. Forget expensive pre-fabricated sheds; with a little elbow grease and these detailed instructions, you'll build a unique and sturdy structure to house your gardening tools, outdoor toys, or anything else that needs a safe and dry place.
Planning Your Pallet Shed Project
Before you dive into construction, careful planning is crucial. Measure your desired shed dimensions, considering the available space in your backyard and the size of the pallets youâll be using. Standard pallets measure approximately 48 inches by 40 inches, so factor this into your design. Sketch a simple plan, noting the number of pallets needed for the walls, roof, and floor. Source your pallets responsibly; ensure they are treated for outdoor use and free from rot or significant damage. Check local regulations regarding the use of reclaimed wood â" some areas may require specific treatments or permits.
Gathering Your Materials and Tools
Essential Materials
You'll need a substantial number of reclaimed wood pallets â" the exact quantity depends on your shed's size. In addition to the pallets, gather the following:
- Strong screws and a drill with various drill bits: Choose exterior-grade screws designed for wood to ensure longevity.
- Pressure-treated lumber for the foundation: This will create a level and stable base for your shed.
- Roofing materials: Choose a material suitable for outdoor conditions â" tar paper, shingles, or even a heavy-duty tarp will work.
- Optional: Exterior paint or stain to protect and beautify the shed.
Necessary Tools
Assemble your toolbox with these essential tools:
- Measuring tape and level: Accuracy is vital for a sturdy structure.
- Hammer and pry bar: For dismantling and assembling the pallets.
- Screwdriver bits (or impact driver): To fasten the screws efficiently.
- Safety glasses and work gloves: Always prioritize safety!
- Circular saw (or hand saw): To cut pallets to size if needed.
Construction: Building Your Pallet Shed
Begin by preparing the foundation. Level the ground and create a frame using pressure-treated lumber. This will prevent rot and provide a stable base. Next, assemble the walls. You can arrange the pallets vertically or horizontally, depending on your preference and the structural integrity of the pallets. Securely fasten the pallets together using screws. For added strength, consider adding corner posts made from the pressure-treated lumber. Once the walls are complete, construct the roof. You can create a simple gable roof using additional pallets or other suitable lumber. Cover the roof with your chosen roofing material to ensure water resistance. Finally, add a door and any desired windows, cutting openings in the appropriate pallet sections. Securely fasten the door and any additional features.
Finishing Touches and Maintenance
After completing the construction, consider adding a layer of exterior paint or stain to enhance the shed's appearance and protect the wood from the elements. Regular maintenance is key to extending the lifespan of your pallet shed. Inspect the structure periodically for loose screws or damaged pallets, and address any issues promptly. Regular cleaning and occasional repainting will keep your shed looking great for years to come. Enjoy your new, charming, and functional backyard shed â" a testament to your DIY skills and resourcefulness!